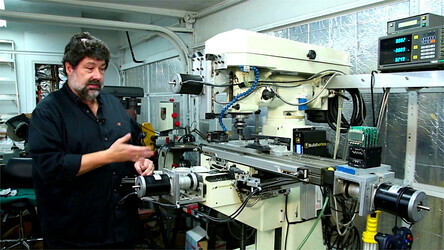
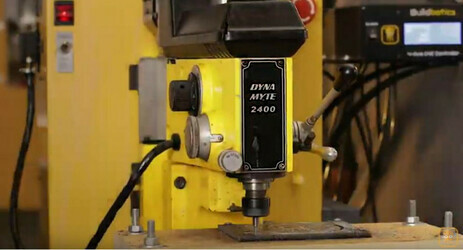
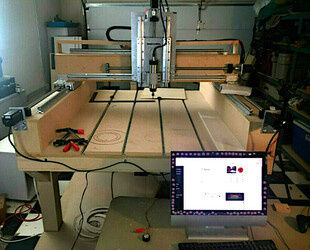
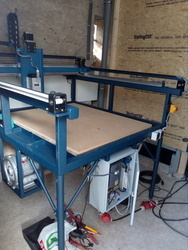
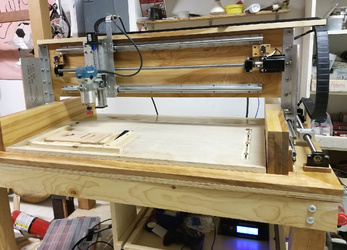
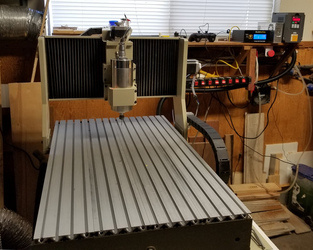
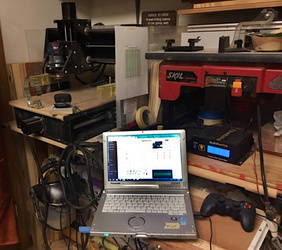
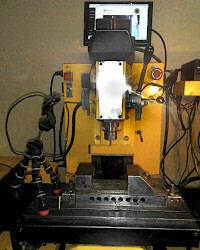
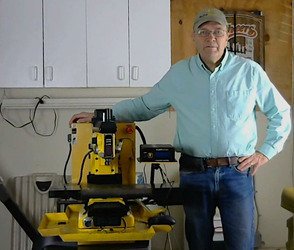
Read an independent product review.
The Buildbotics CNC Machine Controller

The Buildbotics controller is a fully enclosed, smart CNC machine controller with built-in Web interface and advanced GCode processor. It can drive up to 4 stepper motors and many different tools such as a CNC spindle, LASER cutter or plasma torch.
You can buy it now in our store.
Frontpanel
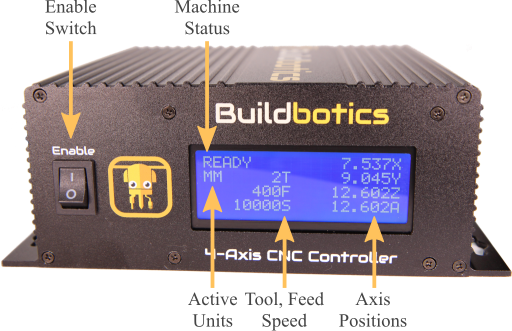
Backpanel

Main I/O Breakout
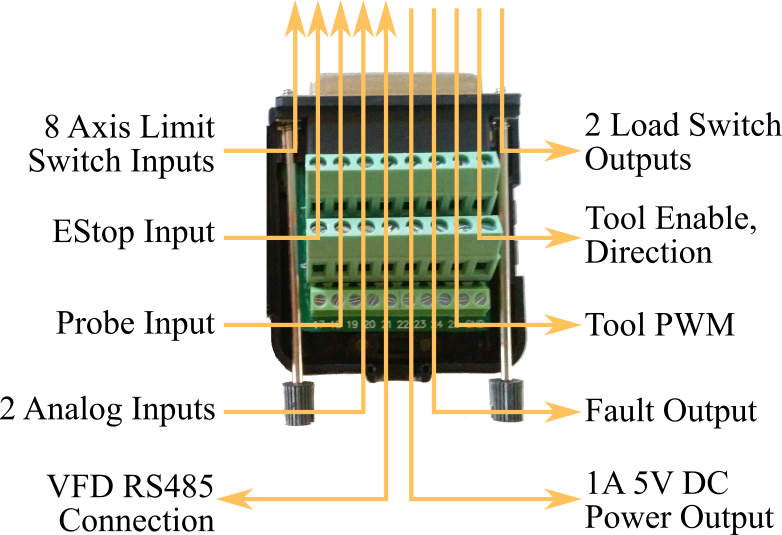
Connect limit switches, Z-axis probing, PWM spindle control, RS-485 spindle control, and e-stop switches easily via the included 25-pin I/O breakout board using simple screw terminals.
Check out the pin-out diagram.
Auxiliary I/O Breakout
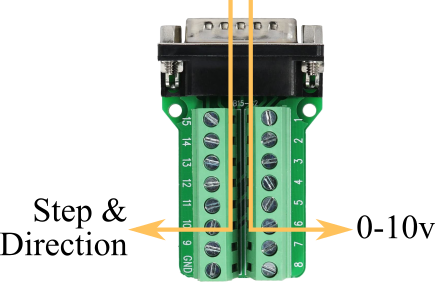
Connect step and direction signals to external motor drivers to use closed-loop steppers or even servo motors with the Buildbotics controller.
Use the 0-10v output to control analog spindles.
Included USB Gamepad
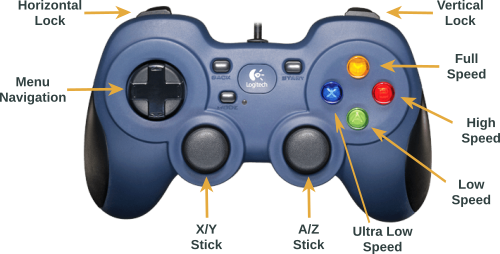
Setup up cuts with ease and agility using the included gamepad.
Included Cables
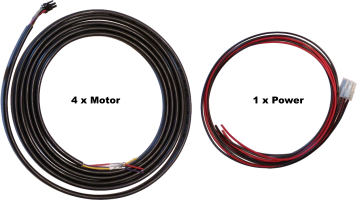
The Buildbotics controller comes with the following time saving pre-made cables:
- 4 x 10 foot (3 meter) Motor cables
- 1 x 4 foot (1.2 meter) Power cable
Optional USB Web Camera
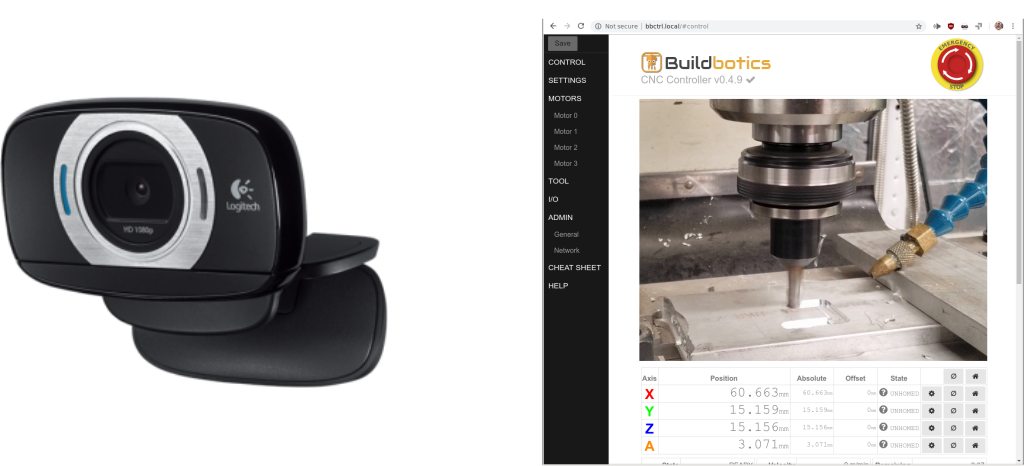
With the optional USB camera you can keep an eye on your CNC from anywhere using a Web browser or smartphone. Add it to your controller package by selecting the option on our store.
Power Supply Options
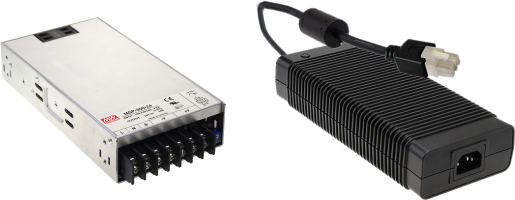
Connect any power supply which outputs 24v to 48v DC with at least 6A using the included power cable select one of our bundled power supply options on our store.
Built-in Stepper Drivers
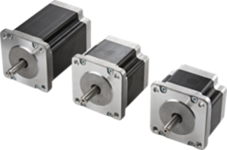
- 4 motor driver channels
- Up to 6A per channel
- 24v to 48v DC
- Up to 256 microstepping
- Smooth S-curve acceleration
- Step rates up to 250k/sec per channel.
Drive most NEMA 17, NEMA 23 and NEMA 34 motors. Preliminary support for 4th axis as a rotary axis. The fourth driver can be synchronized to drive a single axis with two motors. Here's a list of some motors we recommend.
S-Curve Acceleration
S-Curve acceleration is an advanced motion planning algorithm which smooths out CNC movement. Most CNC controllers use trapezoidal acceleration which is much simpler but results in jerky movement that produces rough cuts and increases wear and tear on both tools and the CNC machine itself.
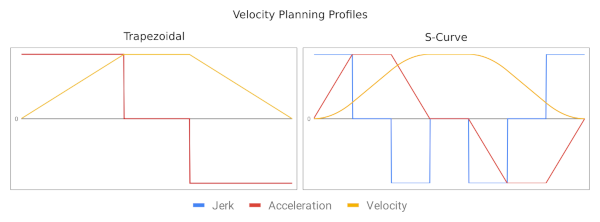
Awesome Technical Support
Get a hold of a real person when you need to. We provide technical support by email, phone or via the Buildbotics forum.
Check out our reviews to see just how much our customers love our technical support.
Have questions?
Email (info@buildbotics.com) or call us (707-559-8539). We are happy to help.
Check out our Reviews
Many of our customers have built new CNCs, converted old ones or revamped their existing machines using the Buildbotics CNC controller. Check out their reviews to see what some of them have to say.
Try the Controller Software Online
Make your CNC incredibly easy to use with the Buildbotics controller's intuitive built-in software.
Upload your GCode and press the play button to run a simulation of the real Buildbotics CNC controller.
See what it's like to configure motor, tool and limit switch settings.
Compatible with most CAM software
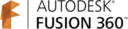

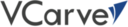

The Buildbotics CNC controller accepts GCode from CAM software like Fusion 360, Mastercam, VCarve, BobCAD, MeshCAM, CamBam, and many others. Test your GCode for Buildbotics compatibility for free with CAMotics.
Reliable Electronics
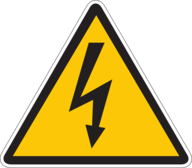
We know you want your CNC to just work when you need it to. Yet, many cheap CNC controllers were designed with little or no attention to electrical safety. The Buildbotics controller is protected from:
- Over-current
- Thermal overload
- Under voltage
- Reverse voltage
- Short-circuit
- Voltage spikes caused by motor stalls
Stay Cool without a Fan
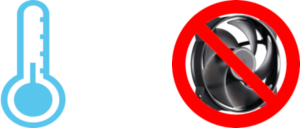
The Buildbotics controller protects against thermal overload. Through careful selection of high-quality electronic components, the Buildbotics controller stays cool, without a fan, even while driving 6A motor loads. Going fan-less not only eliminates noise but also avoids sucking in dust and debris.
Dedicated Computer not Required
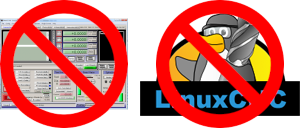
A finely tuned PC running Mach or LinuxCNC is not needed. You can access the Buildbotics controller's built-in software from any of your devices and be sure that your CNC will run smoothly and uninterrupted.
You can even try out your GCodes online with our free demo software.
Fast, Smooth & Accurate Stepping
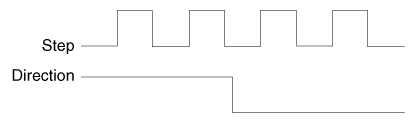
Get maximum performance and accuracy from your CNC. The Buildbotics controller achieves smooth step rates up to 250,000 per second allowing you to use up to 256 microstepping at high speeds.
Wired or WiFi Networking
The Buildbotics controller offers a modern Web interface accessible from a browser over your local network or WiFi. A whole network of Buildbotics controllers can be managed from a single computer.
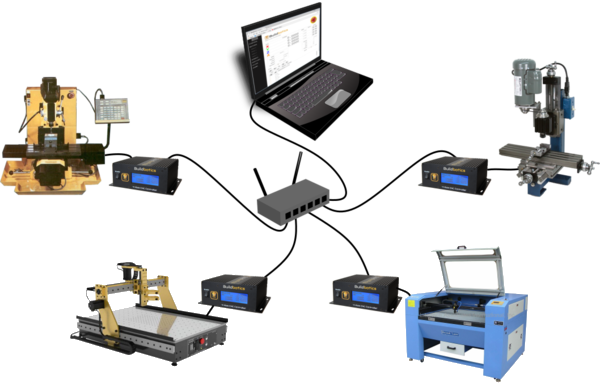
Free Simulation Software
All the software you need to run GCode on your CNC machine is built in to the Buildbotics controller but you can also use our free simulation software to test your GCode before you run it.
The CAMotics CNC simulator computes 3D cut previews from GCode. CAMotics can also send GCode directly to the Buildbotics controller over the network and track the machine position while it runs.
Tool Control
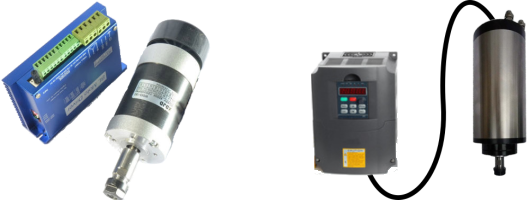
Three different options for controlling external tools, such as spindles:
Drive External Loads
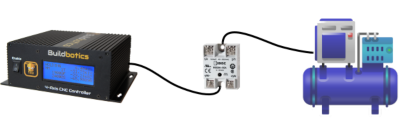
Digital outputs can switch external drivers to control heated beds for 3D printers, extruders, vacuum tables or whatever else you can think of. Switch them on and off from your GCode programs.
For AC loads, an inexpensive SSR switch can be used. External relays can be used for DC loads.
Aluminum Enclosure
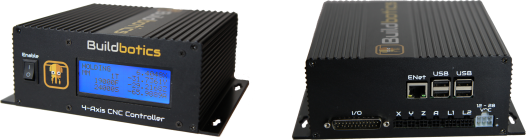
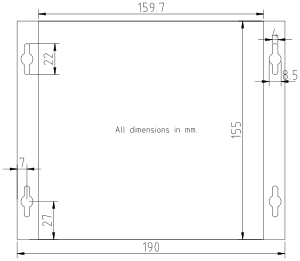
By carefully considering heat throughout the design process the Buildbotics controller dissipates heat through its fan-less aluminum enclosure without sucking in metal or wood shavings.
Four screw holes allow the enclosure to be easily mounted on or near the machine.
RaspberryPi Inside
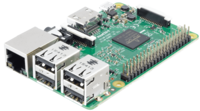
The built-in Raspberry Pi running Linux provides massive potential for building your next big idea. Install additional software on the Pi or use Python code to build new features.
Tested
The Buildbotics controller has been successfully tested in many CNC builds both by us and our customers.

We filmed the construction of a Taig CNC mill, an OX CNC router, a K40 LASER upgrade and a Dyna Myte 2400 retrofit. Check out the videos on our Youtube channel.
Check out some of machines we've build with the Buildbotics CNC controller.
Source Code, Schematics & PCB layout
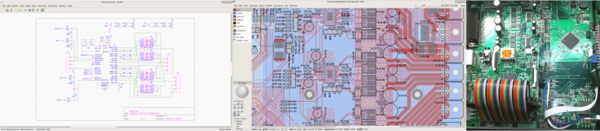
Welcome, software and hardware developers. We’ve already implemented a lot of cool features but we have not even scratched the surface of what this controller could do. That is why we’ve made everything 100% Open-Source.
Here’s what you can find on GitHub: